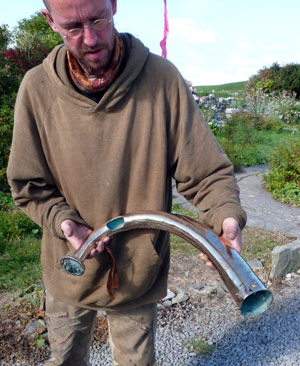 |
Holger Lonze with his casting of
a Bronze Age horn in Doolin Co Clare, Ireland, at the 2010
bronze casting symposium, Umha Aois. |
(originally printed in the East Riding Archaeological
Society News issue No.74, reprinted here with the permission of
the author. All photos by the author.)
I attended the nine day Umha Aois (Irish
for Bronze Age and pronounced Oova Ish) Bronze Casting Symposium
in Doolin, County Clare, on the west coast of Ireland. It is a real
hands-on event and has been held annually for several years.*
The aim of the project is to understand more fully, how Bronze Age
metal working was carried out, by attempting to reproduce items
for which there is artefactual evidence, using, as far as possible,
methods for which there is archaeological evidence. There is also
a certain experimental aspect, looking at methods which could have
been used and which might not necessarily leave any evidence.
*
Editor's Note: Umha Aois has been running annually since 1996
Most of those attending were either sculptors,
metals specialists or archaeologists, although the project started
out originally as an artist/sculptor based event but has gradually
become more biased towards the archaeology. The focus of this
year’s event was on trying to reproduce some of the magnificent
blowing horns dating to the Bronze Age and found in various areas
of Ireland. Many examples of horns, either side-blowing or end-blowing,
are displayed in the National Museum in Dublin, together with
other ritual objects, including crotals, the ovoid, seamless,
hollow, bronze objects, known only from the Dowris hoard and thought
possibly to be associated with a bull cult.
It is thought the horns were made using the
lost wax process, but the work involved in making such a wax model,
together with its sprue assembly was extremely complex. In its
simplest form, the sprue assembly comprises a pouring cup and
tubes for the molten bronze, together with risers to allow the
hot gasses to escape. Many people will perhaps have experience
of using the lost wax method of casting, so I won’t describe
the full process here. However, I will say that applying all the
runners and risers to a large, hollow, delicate wax object such
as a horn requires a lot of skill in assembling it securely, with
minimal handling of the whole relatively soft, but heavy wax object.
Hollow objects such as socketed items or horns are also more complex
because they must have a core, which needs to be held in place
by pins or chaplets, as once the wax has been melted out, the
core will be loose inside the mould. (Needless to say, as a beginner
I did not tackle a horn, but managed to produce a reasonably successful
socketed spearhead, a flanged axe and a couple of smaller items).
The wax models were dipped in two layers of
clay slip, before being built up gradually with layers of clay
mixed with horse dung and some grog, until a good thick mould
was achieved. The wax was then melted out (and collected for re-use)
in two stages. Firstly, over a fire, it was melted from the pouring
cup, thus giving an escape route for the wax deeper inside, and
preventing sideways expansion which might cause the mould to explode.
Further heating of the moulds, placed upside down in a furnace,
melted out all the remaining wax. The clay moulds were then fired
hard in the furnace. The resultant hollow, fired clay and dung
moulds were light and crumbly on the outside and withstood the
heat shock of being filled with molten bronze, whilst the inner
layers of fine clay slip maintained the fine detail of the original
wax model.
The smelting and casting was done either in
simple pit furnaces inside a wood and canvas yurt or in the open
air, in small above-ground, hand-built furnaces which we made
from clay and horse dung. Using lumpwood charcoal, in either of
these furnace types, it took surprisingly little time, with the
aid of the wood and leather bellows, to achieve a pouring temperature
of 1050 – 1070°, which was thought to be suitable for
the type of mould being used. During this project, most of the
bronze was smelted from 90% copper and 10% tin, although when
casting a Medieval style bronze hand bell, 20% tin was used, to
achieve a better ring tone and it did indeed give a beautiful
sound.
About six attempts were made to cast a horn,
but only one was really successful and there is more work to be
done on refining the method. It seems that casting with the mould
supported in the ground in an almost upright position and with
a single pouring cup, thus giving better pressure to the flow
of molten bronze, might be better than placing the mould horizontally
and having multiple pouring cups. However, there are so many variables
that this cannot be stated with certainty. The successful casting
was of a side-blowing horn, which had the typical decoration of
small conical spikes around the open end, and a small loop close
to the closed end. It is thought that the original horns were
probably made specifically for individual persons, as the gap
at the narrow end was nearly always about a hand width, allowing
for comfortable holding when being blown. The successfully cast
horn made a very good sound and was relatively easy to blow, using
closed, vibrating lips. The bullocks in the next field were intensely
interested whenever the horn was blown!
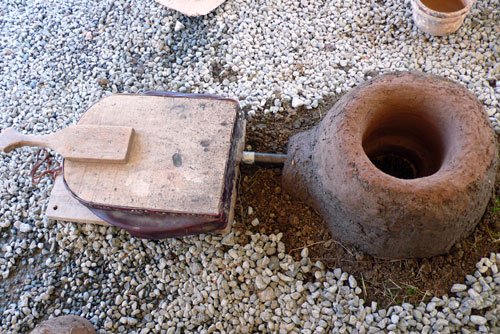 |
Above-ground furnace made
fron clay and horse dung, used with large bellows. |
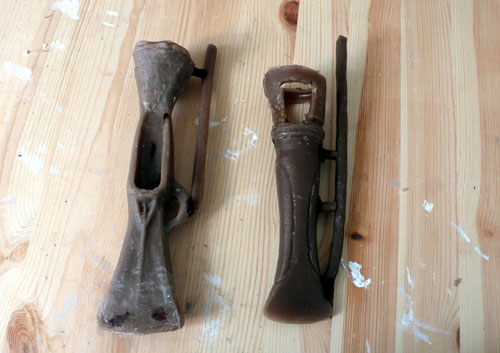 |
Wax models of a flanged axe
and a socketed axe, with partially completed sprue assembly. |
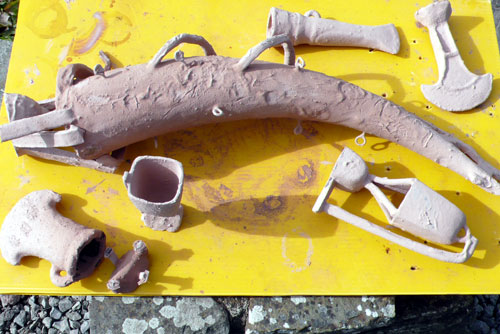 |
Various wax models and their
sprue assemblies drying after their first coat of clay slip,
ie the first stage of mould making. |
 |
Melting out the wax from a
completed horn mould and an axe mould. |
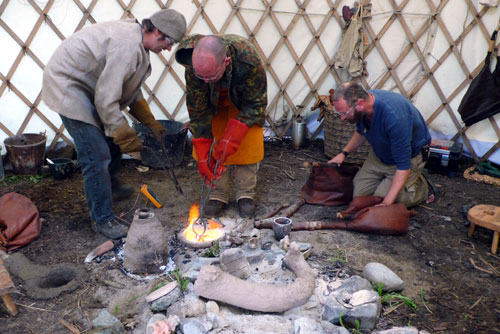 |
Melting bronze in a pit furnace,
to pur into a bell mould. A horn mould also lies in the foreground. |
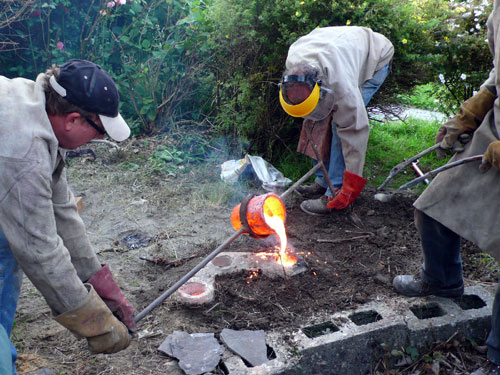 |
Pouring a horizontal horn
mould, made with three pouring cups. |
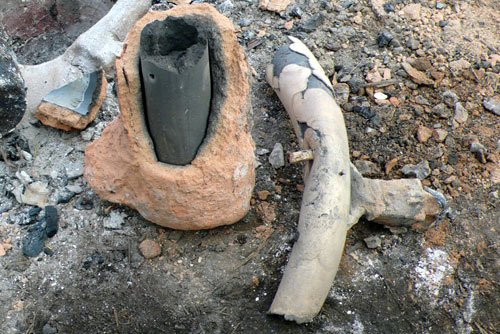 |
An unsuccesful horn where
the bronze has not poured into the wide end of the clay mould.
The clay core can be seen in the unused part of the mould. |
|